Storage and Maintenance Tips for Optimal Biodiesel Performance
- Karen Potratz
- Jun 30
- 7 min read
Updated: Jun 30
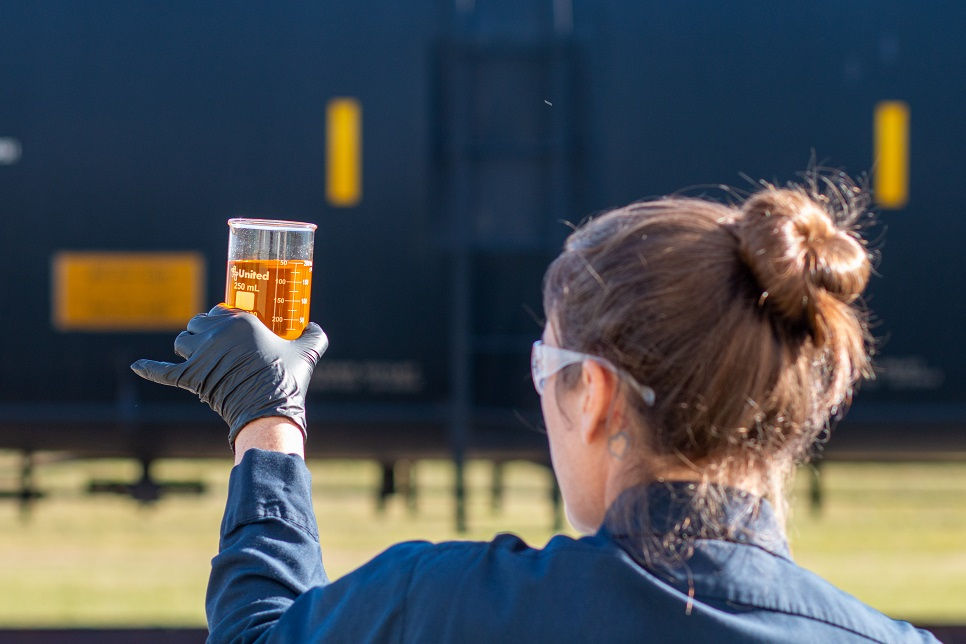
Follow these best practices for trouble-free operations.
Whether you are running on petroleum or biobased fuels, storage and dispensing systems need regular maintenance to ensure optimal fuel performance. Too often, biodiesel is falsely blamed for fuel issues when the real culprit lies within the storage system. Even the best-quality fuel will fail if the tank or dispensing equipment is faulty or contaminated. To avoid problems, always follow these best practices, especially when implementing biofuels for the first time.
Avoid Water Contamination
Water is the No. 1 enemy of fuel quality, corroding tanks, promoting microbial activity and leading to fuel icing during cold weather. Pete Probst, technical director for the Michigan Advanced Biofuels Coalition (MiABC), advises operators to sample fuel tanks at least once per year to visually check for water contamination.
“Electronic tank monitors don’t always convey water levels accurately,” Probst says. “Water is more dense than fuel, so it settles to the bottom of the tank. Therefore, to accurately assess water contamination, it’s important to take fuel samples from the tank bottom. Sample as many access points as possible since tanks may shift after installation and cause water to settle at different parts of the tank.”
Probst advises collecting samples in a clear container to better judge fuel appearance. High-quality fuel should be clear and bright. If the sample is cloudy and hard to see through, it could indicate small water droplets are suspended, or entrained, in the fuel. The amount of moisture that can be entrained in the fuel is called the “saturation level” and is a function of fuel temperature and type.
When entrained water in fuel exceeds the saturation point, it will come out of solution and settle into a layer of free water at the tank bottom. This frequently occurs at the start of winter. Relatively warm fuel can get pumped into a colder vehicle fuel tank, causing any entrained water to drop out. Free water can cause filter icing, corrosion and poor engine performance.
Note that biodiesel tends to have a higher capacity to hold water in suspension compared to petroleum diesel. Regardless, the ASTM moisture content limit of 500 parts per million (ppm) is the same for diesel, biodiesel and biodiesel blends.

Moisture can infiltrate fuel in several ways. Humid air can enter storage tanks through vents as fuel is pumped out. When temperatures drop, the moisture can condense and enter the fuel. Equipment providers offer vent desiccant filters that trap moisture before it reaches the tank.
If cloudy fuel is an issue, talk with your fuel provider or fuel-additive supplier to determine which additive can reduce the entrained moisture.
To prevent water entry, conduct a thorough inspection to find any moisture-infiltration points and repair as needed. Continue monitoring the tank to make sure the water contamination does not return.
Prevent Microbial Growth
The presence of free water in the tank could lead to microbial activity, affecting fuel performance and damaging equipment. Microbes cannot survive without free water.
“Microbial contamination has become more common with the adoption of ultra-low sulfur diesel,” Probst says. “Sulfur has natural antimicrobial properties. Before sulfur was removed from diesel fuel, it acted as a natural deterrent to microbial growth. Also note that microbial activity tends to be more common in warm and humid environments.”
A hazy fuel sample with a sediment that appears soft could be a sign of microbial contamination. The best way to determine microbial activity is to send a fuel sample to a lab that can perform test method ASTM D6974. This test measures colony-forming units and can determine if the microbes are bacteria, fungi or algae. Sampling equipment must also be clean and sterilized with alcohol to prevent cross-contamination or false positives.
If microbes are detected, apply a biocide treatment to kill them, following the product manufacturer’s recommendations. After biocide treatment, prepare for additional filter changes. Tank cleaning or fuel polishing may also need to be considered.
“Severe cases of microbial activity may require the entire fuel system to be drained and cleaned since the microbes can persist and coat the interior tank surfaces,” Probst says.
Inspect Fuel-System Components
Beyond the tank, it’s important to regularly inspect all nozzles, caps, hoses and gaskets and replace them if needed. These components can loosen or deteriorate over time, providing an entry point for water and other contaminants. Spill buckets and sump-pump pits should be inspected monthly. Remove water immediately if detected.
All dispensing equipment and hardware must be properly rated for the biodiesel blend being used, according to Brad Crawford, director of engineered fuel systems at Benecor of Fenton, Michigan. Benecor recently joined MiABC as a stakeholder.

“Biodiesel can accelerate the degradation of certain materials used in fuel-system components,” Crawford says. “Metals such as copper, brass, bronze, lead, tin and zinc can catalyze the breakdown of fuel and cause potential performance issues. These metal components must be replaced with biodiesel-compatible materials before using biodiesel blends.”
Any rusted components should also be replaced or sanded, primed and painted to prevent leaks. Aboveground storage tanks and piping should be painted white to prevent excessive heating from the sun.
Use Proper Filters, Replace Regularly
A properly sized filter installed on dispensing equipment is an economical way to protect diesel engines and help prevent problems.
“Filtration plays a critical role in preserving the quality of any fuel, including biodiesel,” Crawford says. “Selecting the right filter media ensures that particulate matter is effectively removed from the fuel.”
Filters with microglass media are recommended for particulate-matter removal from biodiesel blends up to 100 percent, as well as from ultra-low sulfur diesel, gasoline and ethanol blends up to 25 percent.
If the fuel-filter change intervals are occurring more quickly than normal, check the fuel tank for sediment and consider sending the filter to a lab for analysis. Replace filters at least once or twice a year.
Be aware that biodiesel tends to act as a solvent and can clean the accumulated varnish and sediment from older fuel systems. The loosened materials will get caught in the dispenser filters, requiring filters to be changed more often. After the cleaning action is complete, you’ll be able to resume normal filter-change schedules.
Adjust for Cold Weather
In colder climates, heating elements may be needed in pipes and dispensing hardware to maintain proper flow rates and system performance, especially when using higher biodiesel blends. Since fuel thickens as temperatures drop, consider a larger 30-micron fuel filter during winter months. A fuel’s cold-weather operability and the effectiveness of cold-weather additives should be tested in the lab before winter sets in.
Keep Accurate Records
Regardless of time of year, ensure all workers are trained in safe and proper fuel handling, including fuel delivery. Keep accurate records of training, maintenance, inspections, tests and repairs—for regulatory compliance as well as fuel reliability and trouble-free operation. Sound management practices will support smooth operations, regardless of fleet size and the type of fuel being used.
Biodiesel Assistance Available
For biodiesel users or distributors in Michigan, MiABC has funding and expertise available to help diagnose and troubleshoot fuel-quality issues. Email contact@ miadvancedbiofuels.com for assistance with fuel sampling, training, fuel-quality testing, or any other biofuel questions.
Sidebar: Underground or Aboveground Tanks—What’s Best?
For those considering a new biodiesel storage system, an important decision must be made about the type of fuel tank to install. Understanding the differences between underground storage tanks (USTs) and aboveground storage tanks (ASTs) will help determine the best fit. The choice between USTs and ASTs depends on multiple factors, including site layout, environmental conditions and fuel blend.
“Regardless of the storage system you select, it’s important to consider component compatibility, heating requirements and equipment certification to ensure safe, efficient and trouble-free biodiesel operations,” says Brad Crawford, director of engineered fuel systems at Benecor.
USTs offer the advantage of temperature stability. Soil temperatures typically average around 50 degrees Fahrenheit at a tank depth of 10 feet. This natural insulation often eliminates the need for heating equipment, even when storing high blends of biodiesel. But operators must be aware of the need for rigorous maintenance and regular inspections to avoid potential environmental impacts from USTs.
On the other hand, ASTs are generally more cost-effective to install and easier to maintain. They also offer site flexibility and the ability to relocate or expand the storage system if needs change in the future. ASTs, however, must be equipped with insulation and heating systems to accommodate the higher cloud point of biodiesel blends of B30 up to B100. To prevent gelling or flow issues, storage-tank temperatures need to be maintained at 5 degrees to 10 degrees F above the fuel’s cloud point.
“When purchasing a new storage tank, whether underground or aboveground, evaluate every component of the fuel system to ensure compatibility with the biodiesel blends you plan to use,” Crawford adds. “This includes dispensing equipment, piping, motors and seals.”
Parts made from Teflon®, Viton™, fluorinated plastics or nylon will extend longevity and resist fuel-induced swelling or degradation. Keep in mind that many states require full documentation of all components at the time of tank installation. Consult the fuel-tank manufacturer or distributor for guidance on biodiesel-compatible components.
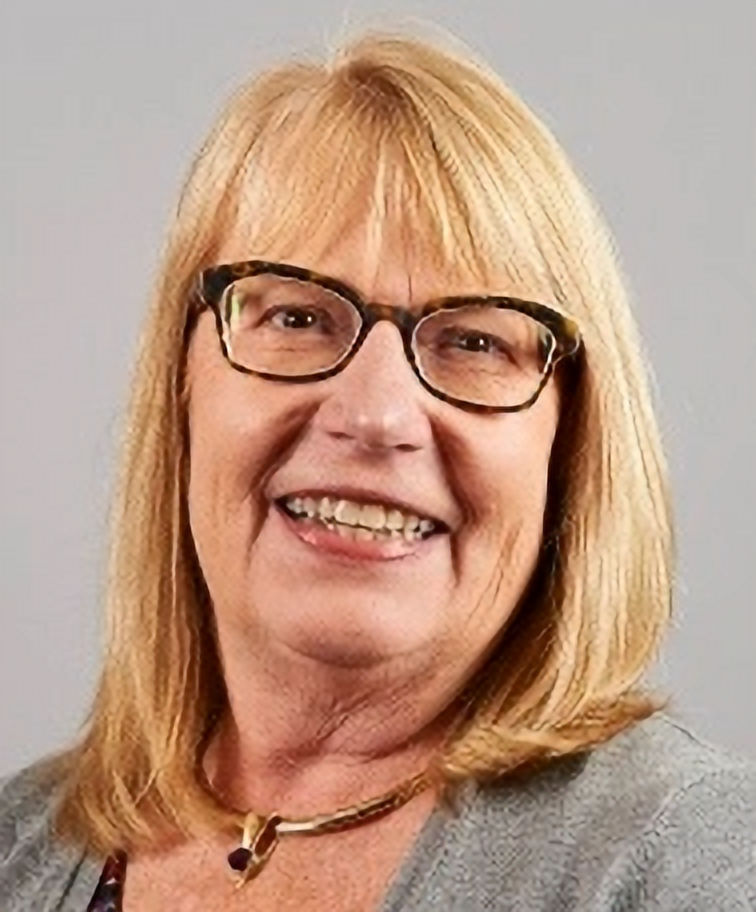
Author: Karen Potratz
Communications Director
Michigan Advanced Biofuels Coalition
262-470-3709